精益生產現場管理通過消除浪費、優化流程和持續改進,能為企業帶來多方面的核心價值提升,以下是其主要好處及具體表現:
?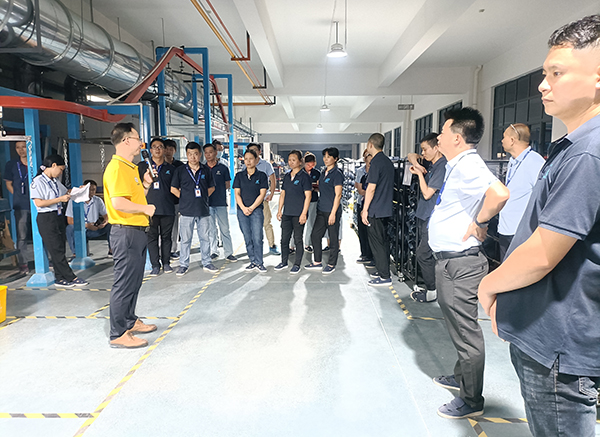
一、顯著降低成本,提升利潤空間
消除七大浪費
減少生產過程中的過量生產、庫存積壓、等待時間、搬運損耗、不良品返工、動作浪費、流程冗余等無效活動,直接降低人工、物料、設備能耗等成本。
案例:某汽車零部件工廠通過優化生產線布局,將搬運距離縮短 70%,年節省物流成本超百萬元。
降低庫存成本
采用 “拉動式生產”(JIT)模式,根據實際需求生產,避免庫存積壓,減少倉儲空間占用和資金凍結。
數據:豐田推行精益后,庫存周轉天數從 30 天壓縮至 3 天,庫存成本降低 80% 以上。
二、提升生產效率與交付能力
優化流程與布局
通過 “價值流分析”(VSM)梳理流程,合并冗余環節,減少無效等待和動作,提升單位時間產出。
示例:某電子廠將傳統 “孤島式” 生產線改為 “單元式” 布局,生產周期從 48 小時縮短至 12 小時。
快速響應市場需求
小批量、多品種的柔性生產模式,支持快速切換產品型號,縮短交貨周期,提升客戶訂單交付準時率(通??蛇_ 95% 以上)。
三、保障產品質量與一致性
建立全過程質量控制
通過 “自動化”(Jidoka)和 “防錯法”(Poka-Yoke),在生產源頭檢測缺陷,避免不合格品流入下工序,降低不良率。
數據:某家電企業引入防錯裝置后,裝配錯誤率從 0.5% 降至 0.05%,客戶投訴減少 90%。
持續改進文化
鼓勵一線員工參與 “改善提案”(Kaizen),針對質量問題及時優化工藝,形成 “全員質檢” 的良性循環。
四、強化現場安全與員工管理
打造安全有序的作業環境
通過 “5S 管理”(整理、整頓、清掃、清潔、素養)規范現場物料、工具擺放,減少安全隱患(如通道堵塞、設備故障),降低工傷事故率。
效果:實施 5S 的工廠,安全事故發生率平均降低 60% 以上。
提升員工技能與參與感
推行 “多能工培養” 和 “標準化作業”,使員工掌握多崗位技能,增強崗位靈活性;同時,通過小組改善活動(如 QC 小組)提升員工歸屬感和創造力。
五、增強企業競爭力與可持續性
適應市場變化的靈活性
精益模式幫助企業快速應對市場需求波動、技術迭代和競爭壓力,例如新能源汽車行業通過精益轉型,實現從傳統燃油車到電動車的快速產線切換。
樹立優質企業形象
高效、整潔、低浪費的生產現場成為企業的 “隱形名片”,更容易獲得客戶(尤其是國際大客戶)的信任,提升訂單獲取能力。
支撐長期戰略落地
精益思想與數字化轉型(如智能制造、物聯網)結合,可進一步提升生產智能化水平,為企業向 “燈塔工廠” 升級奠定基礎。